University of Wyoming Project Walk Through
Every design/build project has it’s problems that need to be solved and this project had more than it’s fair share.
Skylight Design/Build Problem Solving
Every time we evaluate a project we always look at all problems, assess the priority levels of each issue, and then determine which needs to be solved first. The first issue we had to deal with this project was weather. The university is located in Laramie, WY and there is a very short time frame for outdoor work due to weather conditions. The concern for weatherproofing on this project is even bigger with the unique configuration of this particular roof.
The art of problem solving is something we live for here at Skylight Specialists, Inc. We enjoy the design/build process and take pride in providing a job well done.
The need for having product on hand at the right time was critical for job completion. If the product could not be delivered on time then the entire project would have to be put off for a whole year. Needless to say, that is a critical problem. Most skylight manufacturers did not even provide a bid because they could not solve this issue. They thought was no way a quote could be provided and accepted, then the shop drawings completed, evaluated, revised and approved, then the time frame for the construction of the skylights and finally the delivery time. It was a lot to solve in a short period of time.
Site Built Skylights Compared to Pre-manufactured Skylights
We avoided the issue and wasting all that time by providing a site built glazing system called MAGS BAR. Along with the ready availability, the product is also capable of being designed to sit flush to the new roof system being applied without changing any of the internal structure. We worked closely with the contractor and the University of Wyoming to insure the design would work as requested.
The custom application was also convenient because each skylight had different angles and shapes. We were able insure a proper fit with each and every skylight. A pre-measured skylight cannot guarantee a skylight to be pre-manufactured to fit. It is a big problem when product arrives and doesn’t fit as expected ,usually because after demolition the building’s details were not as expected.
Protecting Interior Spaces from the Elements
As in all projects that require a skylight replacement, protecting the interior space from water penetration during the work is an issue. The contractor specified 100% no water penetration on this project, it was critical we create a solution. As we removed the existing skylights and started the work needed to install the MAGS BAR, the contractor had the responsibility to cover and uncover the openings every day using plywood and ice and water seal. However, these temporary covers could not be applied quickly for fast moving rain showers during the day and were costly to provide.
Our solution was to provide a rolled up EPDM rubber roofing at the top of each opening that could be quickly rolled over the opening during surprise rain showers. This solution worked very well and did not take as much time as covering the openings with plywood and ice and water seal everyday as the contractor previously specified. It worked so well that it was used throughout the entire project, saving time and money.
Large Glass Skylights
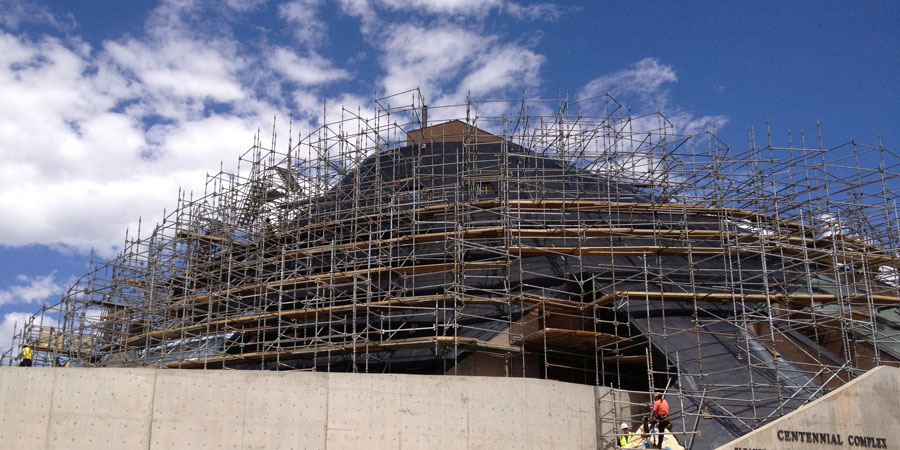
The original design of the glass skylights had openings as wide as ten feet. The problem here lies with the weight of each glass unit. For this project the weight of each unit would prevent being able to manually set them. Additionally, the scaffolding surrounding the entire roof could not hold the weight of glass in crates, preventing manually setting any glass units of a smaller size. And the University of Wyoming did not want to change the look or the perimeter structure of the openings or the shape and size of each skylight.
The solution was to set all the glass with cranes and a tool that can be hooked to the crane and suction-cupped to the glass. Each piece of glass was removed from its crate on the roof, cleaned and prepared for craning to its final resting space. The glass was threaded down through layers of scaffolding and set in place. This process, although complicated, was performed flawlessly and in a timely manner that allowed the glazing to be applied quickly and efficiently.
Effective Design/Build Solutions
As with all our solutions, both on this project or anywhere else we might work, our goal is to complete each under budget and early. Each problem is approached with providing a solution that saves time and money while providing a permanent solution. The last thing any owner or contractor wants is a temporary solution or for the solution to cause a different problem. We make sure that 100% of our projects are successful.